Semiconductor
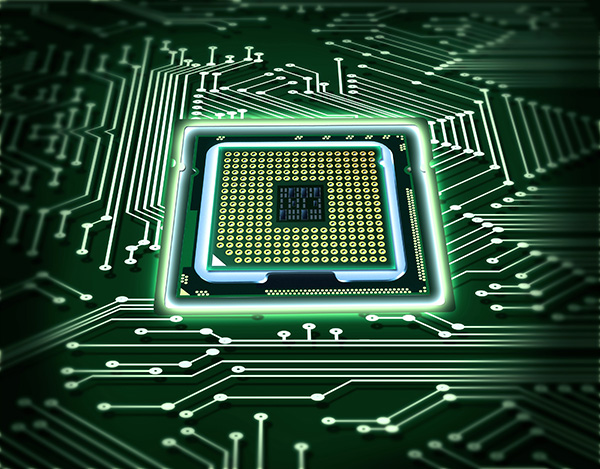
Smartphones, laptops, smart watches, digital cameras…. all of these devices that are critical in the modern economy rely on small electronic parts to run. As demand for these devices has grown, the semiconductor manufacturing industry has thrived. To create the electronic parts in smartphones, digital cameras, laptops, and more, the semiconductor manufacturing industry relies on a number of inert gases. Nitrogen, Argon, Helium, and CO2 are among the most common gases used in manufacturing plants.
These gases have a range of uses. Some etch the electronic parts while others deposit materials on them. Nitrogen gas is used to purge glove boxes or semiconductor chambers, which ensures the purity of the environment. Since nitrogen gas is heavier than air, it will push air out of the environment, creating an oxygen-deficient state. This is beneficial in semiconductor manufacturing as it ensures the environment is sterile and prevents certain materials from interacting with oxygen.
Many semiconductor manufacturing facilities have invested in nitrogen generators or nitrogen dewars which promise a steady supply of nitrogen on demand. When the gas and supply lines are working properly, workers can enjoy nitrogen on demand to keep productivity high. If a leak develops in the supply lines or the generator, nitrogen gas can leak into the plant, where it will start to push oxygen out of the room. While this trait makes nitrogen so useful in manufacturing, it poses a danger by creating an atmosphere that oxygen-deficient.
When room air does not contain enough oxygen, your employees will experience respiratory distress and even death. Other substances used in semiconductor manufacturing can cause severe injury, too.
All of these gases are colorless and odorless, so there is no way for employees to tell if there’s a leak. These gases pose health hazards for employees, and OSHA regulations require that workplaces protect employees from exposure to these gases and provide sufficient notification to make staff aware of the hazards of a gas leak.
To comply with OSHA regulations, semiconductor manufacturing plants must install oxygen monitors to detect levels of oxygen and provide sufficient warning if nitrogen, or any other gas, leaks into the plant environment. Once installed, these monitors take continuous readouts of the room air. As long as there’s enough oxygen, the monitors stay silent. A digital display allows employees to check oxygen levels at a glance, providing verification the facility is safe. If a leak occurs, the monitor will sound a 90-decibel alarm at two levels, 18 percent and 19.5 percent. This protects staff and ensures that the plant complies with regulations regarding the use of oxygen deficiency monitors in environments where inert gases are used.
By installing monitors throughout the site, for instance using a monitor on the manufacturing floor where the cryogenic gases are kept, your facility can protect employee health and comply with existing regulations. Posting signs throughout the facility reminds staff of the danger of leaks and the need to handle materials properly to protect health and safety.
While there are many different types of oxygen monitors, they differ in technology and life expectancy depending on sensors used. O2 monitors from PureAire come with a 3-year warranty and last for 10 or more years without maintenance or calibration. This is in sharp contrast to many other styles of oxygen monitor, which must be calibrated and maintained to provide accurate oxygen readings. PureAire’s oxygen monitors are impervious to changes in barometric pressure, so they will continue to take reliable readings even if there’s a thunderstorm. Deliver peace of mind to your employees and protect your facility by investing in reliable, long-lasting oxygen monitors from PureAire. Browse for your O2 monitor today.