Gas Chromatography
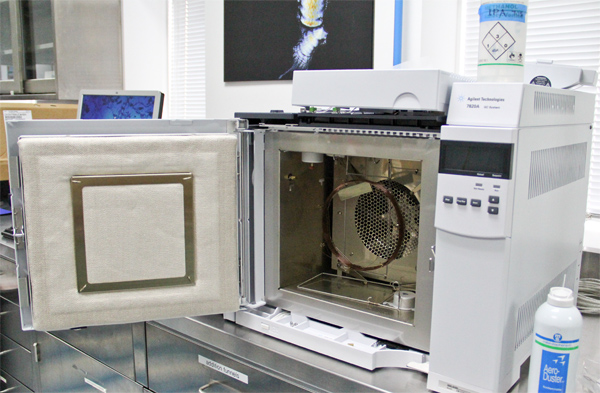
Forensic science, medical research, and other industries need to separate chemical compounds for analysis through a process that’s known as gas chromatography. Inert gases are the engine that drive gas chromatography, because they help to separate out the different compounds so they can be analyzed, but they also pose a risk that personnel must understand.
In gas chromatography, inert gases such as nitrogen pass over the substance being analyzed and separate the material into its component parts for identification. Since the components must be separated, the material that’s serving as the carrier gas — the engine of the process — cannot interact with the component materials in any way. Inert gases are unique in that they do not react with substances being analyzed, so the components of the compound remain pure.
Gas chromatography is a growing industry with untapped potential. Within the agricultural industry, for example, gas chromatography has the potential to improve reliability in medicinal marijuana by indicating whether pesticide residues affect a crop. While the medical marijuana industry does not yet have regulations around pesticide use, this may change as the industry matures. In farming, gas chromatography can check the purity of a substance and ensure there’s nothing harmful to consumers in, for instance, an edible grain.
A few of the gases used in gas chromatography include helium, nitrogen, and argon. These gases all have no color and no odor, and they are all naturally dense. This property leads to a potentially dangerous situation if the carrier gas leaks from the supply line or if a cylinder of gas becomes compromised while in storage or transit.
Because these carrier gases are denser than oxygen, they push oxygen out of the air, creating room air that doesn’t have enough oxygen to support laboratory workers, who rely on oxygen to breathe. With only a couple of breaths of oxygen deficient air, employees could become disoriented, fall into a coma, or asphyxiate. While gas chromatography is safe so long as all equipment is operating properly, a leak in the supply lines could cause serious injury and death to anyone in the facility.
Gas chromatography facilities can protect workers from leaks of carrier gases by using oxygen monitors to track levels of oxygen in the room. The monitors go off when oxygen falls too low, providing sufficient notice for employees to evacuate before suffering respiratory problems. Oxygen monitors from PureAire have two user-adjustable settings — 18 percent and 19.5 percent — to comply with OSHA regulations around gas leaks and help employees exit the facility and avoid getting sick.
Gas chromatography sites should plan to use an oxygen monitor anywhere a carrier gas is stored or used to prevent a hazardous gas leak from threatening the safety of workers onsite. Facilities should also educate workers on the importance of handling gas storage cylinders with care, since improper handling could cause a leak or explosion, damaging the property and harming employee health.
PureAire offers some of the industry’s leading oxygen monitors. Unlike other brands on the market, which must be calibrated regularly to ensure accuracy, oxygen monitors from PureAire need no calibration or maintenance after installation. They will operate for 10 or more years, thanks to a zirconium sensor. PureAire’s oxygen deficiency monitors are ideal for use in confined spaces, such as storage closets or basements, continue to operate in temperatures as low as -40C, and are among the most cost-effective O2 monitors available on the market.
Protect your company and your employees and gain peace of mind by adopting best in class oxygen monitors from PureAire. Browse O2 monitors today.