Cryogenic Gases
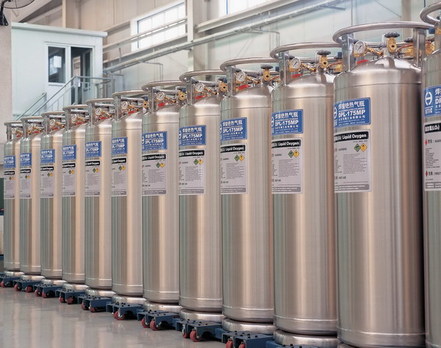
Cryogenics relies on inert gases, including nitrogen, helium, and argon, to maintain very cold temperatures. Many different facilities use these gases, including sports medicine facilities, culinary institutions, cryo health facilities, food processing plants, laboratories, hospitals and medical settings, and more.
These gases create ultra-chill temperatures to help keep tissue and blood properly chilled so they can be used in hospitals and laboratories. They use nitrogen in cryotherapy health centers to reduce inflammation in sports health. They flush oxygen from the environment to sterilize equipment and block bacteria growth in food processing plants, food and beverage industries, culinary institutions, universities, pharmaceutical labs, and other venues.
Nitrogen gas, in particular, is commonly used because it’s easy to produce with a nitrogen generator, which extracts nitrogen from the air, where it’s naturally found.
While some facilities have onsite generators to create nitrogen on demand, other institutions bring in cylinders of nitrogen, which they can use as needed.
No matter how it’s produced, used, or stored, nitrogen and the other inert gases do pose a health risk if they leak out of the supply line or storage cylinder. Inert gases have no color or odor, so there’s no way to detect a leak without an independent monitor. If a leak does occur, inert gases can deplete oxygen from the air. With only a few breaths of oxygen deficient air, people could fall unconscious or die. With cylinders of inert gas, there’s an additional risk of explosion if the cylinder is mishandled, dropped, or not properly stored. Such an incident could claim lives and cause serious damage to the facility.
Educating employees on the dangers of working with inert gases helps reduce the risk of improver handling. However, it’s not enough. Existing regulations require that facilities that use cryogenic gases take action to protect public safety by notifying employees of the risks of a gas leak, training employees in how to respond to leaks, and installing technology that detects and alerts employees to gas leaks before the air becomes deficient of oxygen.
The easiest and most cost-effective way to detect gas leaks is with an oxygen deficiency monitor, a wall-mounted monitor that detects levels of oxygen in the environment. Since inert gases deplete oxygen from the environment, it’s possible to detect a leak by watching for declining oxygen levels.
As long as there’s ample oxygen, the monitor remains silent. Employees can check the digital display for confirmation everything is safe. If oxygen levels fall to critical levels, defined by OSHA as 19.5 percent, the oxygen monitor triggers an alarm to notify anyone in the area to evacuate.
Install oxygen monitors anywhere cryogenics gases are used or stored to have prompt notification if a leak occurs and to come into compliance with existing regulations. PureAire offers a long-lasting, cost-effective line of oxygen monitors built with zirconium sensors. These sensors are impervious to drops in barometric pressure, which means they will perform reliably even if there’s a weather event. While some models of O2 monitor require regular calibration to work effectively, PureAire’s oxygen monitors are designed to work effectively from installation for 10 or more years with no calibration or maintenance. Simply mount the unit on the wall, set it up, and rely on the product to check oxygen levels, provide accurate readouts, and sound the alert in case of leaks. PureAire’s oxygen monitors perform in confined spaces such as supply closets as well as in freezers, and are built to maintain accurate readings in temperatures as low as -40C.
Oxygen monitors provide reassurance for workers, ensure regulatory compliance, and protect your facility from the health risks that accompany inert gas leaks. Explore PureAire’s leading line of oxygen deficiency monitors.