Additive Manufacturing
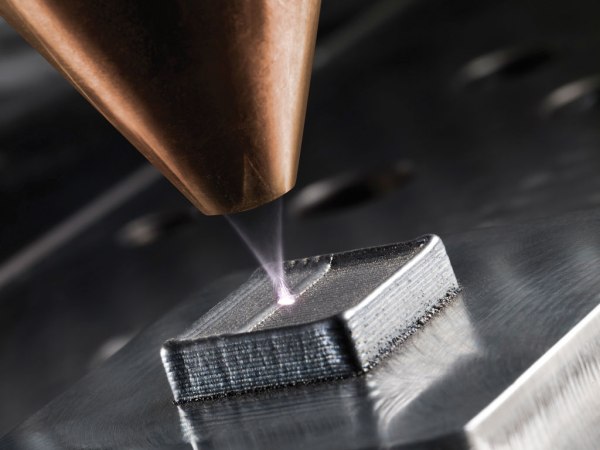
In additive manufacturing or AM, 3D printers can create parts for technology, medical, aerospace, defense, consumer electronics, and other industries using templates. Some of the companies that rely on 3D printing to create devices and components for industries include 3D Systems, Renishaw, and Stratasys.
The additive part of additive manufacturing refers to the way that individual layers are fused together: Powders are deposited in layers, then fused together with inert gases. Argon and nitrogen gas are frequently used. While these gases are safe to use as long as they are contained in the 3D printer, they pose a health risk if they leak into the environment.
So the facility can operate at maximum productivity, many additive manufacturing companies install nitrogen tanks or nitrogen dewars onsite. These cylinders allow the company to draw argon for use in 3D printing. The storage of argon or nitrogen gas represents another potential site of leaks. The facility must take action to protect staff from gas leaks anywhere on site, which means mitigating leaks whether they arise in a faulty 3D printer, in storage cylinders, or from the series of valves and piping.
Both argon and nitrogen gas are denser than oxygen, and as a result they displace oxygen in the environment. If a leak were to develop, oxygen levels in the room would decrease to the point where workers would be confused and dizzy, ultimately falling into a coma or experiencing death by asphyxiation.
Adding to the dangers of a gas leak is the fact that neither argon nor nitrogen gas can be seen or smelled. Thus, there is no way that employees can detect a gas leak using their senses.
Given the critical risks of a gas leak and the inability of employees to detect such a leak, it’s critical that additive manufacturing facilities use technology that is capable of detecting oxygen levels and notifying employees of gas leaks before oxygen levels fall to the point where cognitive or respiratory problems occur. Best practices for detecting and alerting employees to gas leaks are to use oxygen deficiency monitors anywhere inert gases are used or stored.
Wall-mounted oxygen deficiency monitors track the levels of oxygen in the additive manufacturing plant. As long as there’s no gas leak, oxygen levels hover around 21 percent, which correlates to the amount of oxygen naturally found in the air. If argon or nitrogen leaks, oxygen levels will begin to drop. If oxygen falls to the critical threshold defined by OSHA, which is 19.5 percent, the oxygen deficiency monitor will trigger an alarm.
Additionally, many argon 3D printers ideal environment inside the printing chamber is 500ppm or less of oxygen. With low oxygen levels it is important to detect and alert if the gas gets above the maximum threshold. This detection is used with an oxygen analyzer, PureAire offers a 0-1000ppm sensor in addition to the safety oxygen deficiency monitors. Low oxygen is important inside the printing chamber to reduce oxidation in the layer deposition process as well as it creates a non-combustible environment while using highly flammable metals like titanium.
PureAire offers an industry leading oxygen monitor, which comes with a zirconium sensor that lasts for 10 or more years. Unlike other brands, PureAire’s oxygen monitors need no calibration or maintenance once they are installed.
Not only are PureAire’s oxygen monitors low-maintenance, they’re easy to set up and use, which saves time. PureAire’s O2 monitors function accurately even when there’s a thunderstorm altering barometric pressure or when operated in a confined space, such as a storage closet. Accuracy is critical to performance, as inaccurate oxygen monitors can lead to dangerous exposure to oxygen deficient air.
If you’re seeking an oxygen monitor that is cost-effective and long-lasting, you will like PureAire’s products, which come with a 3-year warranty. Explore all oxygen monitors and oxygen analyzers now.